Embarking on the journey of renovating your floors or walls is a significant step towards rejuvenating spaces that authentically mirror your style and identity. However, amidst a plethora of options saturating the market, a pivotal question arises: how can one discern the most suitable choice? This quandary often arises when weighing the utility of ready-to-use microcement against alternatives such as polished concrete or polished cement.
To make an informed decision, it’s imperative to grasp the disparities among these materials. Delving into these distinctions not only aids in selecting the finish that aligns best with your aesthetic and functional requisites but also unveils novel avenues for enhancing your spaces’ allure.
Thus, at Cementec, we deem it crucial to delve deeper into this subject to dispel any lingering uncertainties. In this discourse, we shall navigate through the pivotal disparities among polished concrete, ready-to-use microcement, and polished cement. Furthermore, we shall furnish comprehensive insights into why ready-to-use microcement might emerge as the optimal choice for your needs.
Curious to learn more? Join us as we explore further!
Unveiling polished concrete
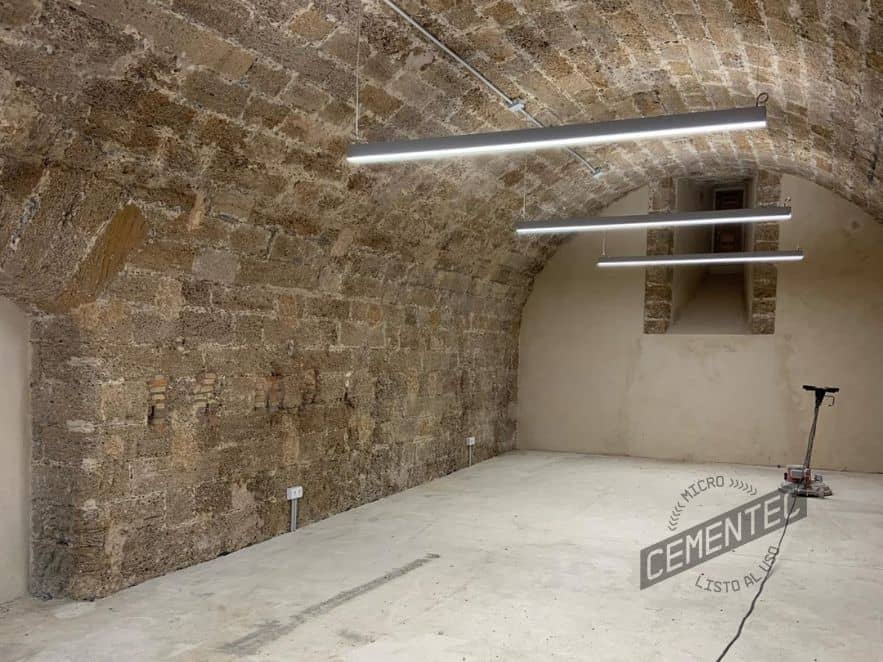
Polished concrete represents a widely employed masonry material primarily comprised of crushed stone, rock, and sand, with a cement content typically ranging between 10% and 15%.
However, what sets polished concrete apart is its finishing process, wherein the surface undergoes meticulous polishing to attain a sleek and lustrous appearance. This process employs specialized tools to eliminate imperfections, unveiling the aggregate and cement in their most refined state.
The quality of concrete hinges significantly upon achieving the appropriate balance of water, aggregates, and cement during the mixing phase. Excessive water can compromise the concrete’s structural integrity, while insufficient water impedes the mixing process. Thus, striking the right equilibrium is imperative to achieve an optimal outcome in terms of both durability and aesthetics.
Distinguishing polished concrete from polished cement
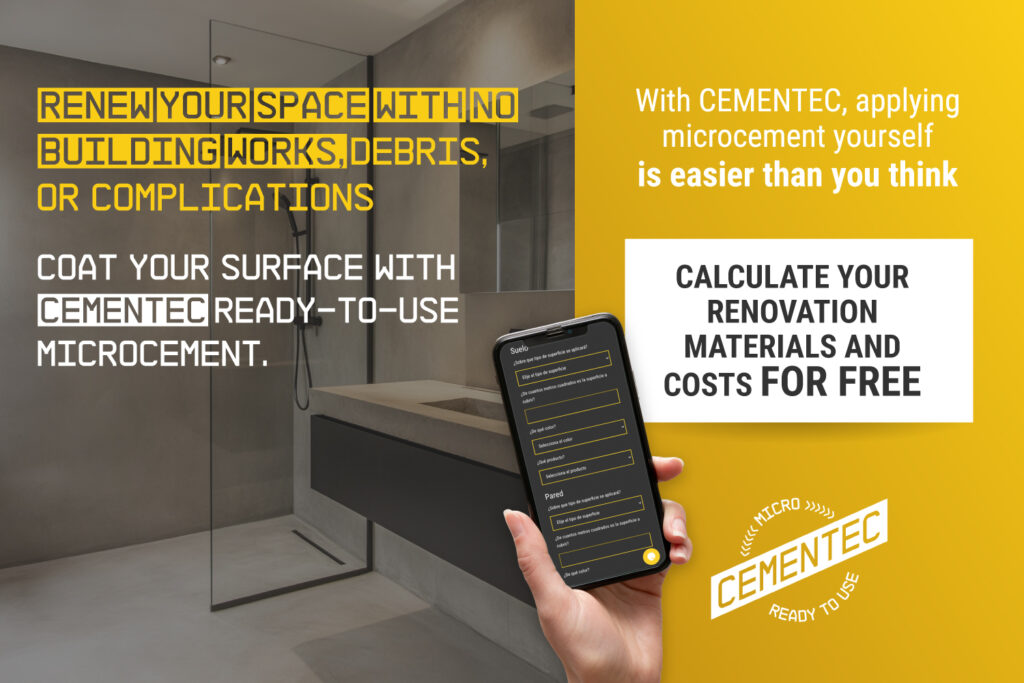
Having previously explored the disparities between microcement and polished cement, let us now delve into the distinctions between polished concrete and polished cement themselves:
– Composition:
- Concrete comprises a blend of cement and aggregates, including crushed stone, rock, sand, and water.
- Conversely, polished cement derives from a mixture of limestone, clay, iron, and other minerals, from which clinker is extracted. This clinker is then ground with gypsum to yield cement.
– Application:
- Polished cement can serve as a standalone construction material, whereas polished concrete necessitates the inclusion of cement in its mix to ensure strength and durability.
– Finish:
- Polished concrete is characterized by its glossy and smooth finish, achieved through a specialized polishing process.
- In contrast, polished cement may offer a variety of finishes but typically appears rougher and less lustrous compared to concrete.
– Versatility:
- Concrete finds applicability in a myriad of indoor and outdoor settings, spanning from floors to walls.
- Conversely, polished cement primarily serves as a floor covering.
– Durability:
- Both materials boast durability, yet concrete tends to exhibit greater resistance to stains and wear.
Bridging the gap: polished concrete versus Ready-to-Use microcement
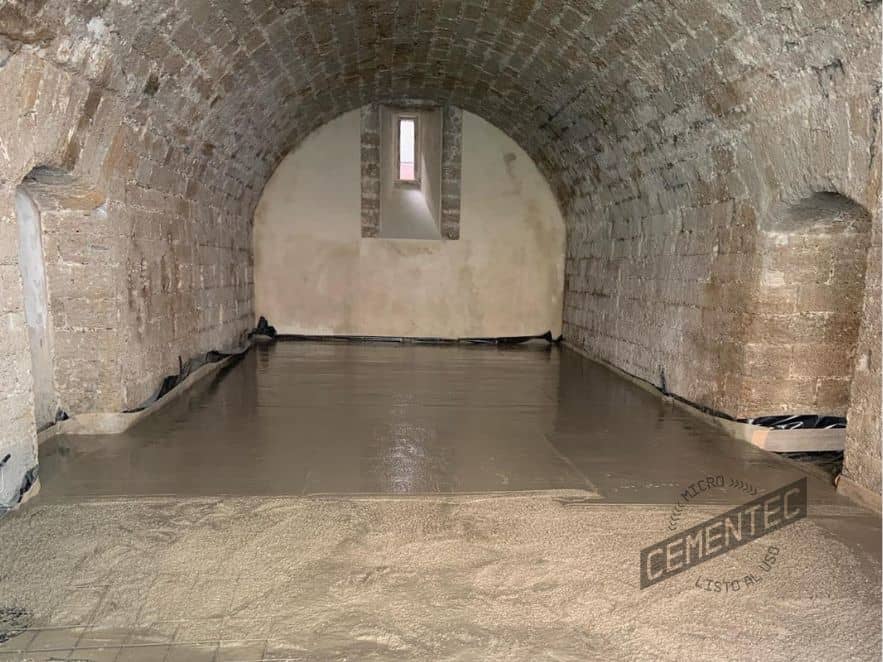
Having elucidated the disparities between polished concrete and polished cement, let us now juxtapose polished concrete with ready-to-use microcement, offering a versatile and contemporary alternative for design and renovation endeavors.
1. Composition
Previously, we delineated the composition of polished concrete, comprising cement and various aggregates. Conversely, ready-to-use microcement distinguishes itself by blending cement with polymers, additives, and pigments, affording unique attributes of flexibility and resistance, particularly against cracking in areas subject to structural movements.
2. Application process
Likewise, the application process diverges between polished concrete and ready-to-use microcement. While concrete entails pouring the mixture into the desired area followed by meticulous polishing, ready-to-use microcement is applied in thin layers atop an existing surface, facilitating adaptation to diverse areas and enabling the creation of personalized decorative effects.
Interested in applying microcement to your renovation project? Learn how to do so effortlessly in four simple steps.
Tomás Amat, architect, creative and manager of Cementec
3. Appearance and Finish
Furthermore, polished concrete stands distinguished by its glossy, refined finish, while ready-to-use microcement offers a plethora of finishes, ranging from matte to satin, vintage, and even rough textures. This versatility extends to the incorporation of pigments, enabling an infinite array of colors and decorative effects.
4. Versatility
Ready-to-use microcement eclipses its counterparts in terms of versatility in application and design. Unlike polished concrete, which may encounter limitations in residential settings due to weight considerations and expansion joint requirements, ready-to-use microcement excels in creating seamless surfaces devoid of visible joints, rendering it ideal for diverse architectural applications.
5. Maintenance and care
Lastly, maintenance of polished concrete typically entails periodic application of sealing coats to safeguard against stains and damage, whereas ready-to-use microcement may necessitate simpler, occasional upkeep such as routine cleaning with mild, non-abrasive products, albeit requiring periodic sealing as well.
Summary: polished concrete vs. Ready-to-Use microcement
- Concrete requires more logistics and preparation.
- It is not feasible to use polished concrete in buildings from the first floor upwards, as the weight of the material is very high, complicating its application at height.
- Concrete must have expansion joints every 25m2 to accommodate its significant expansion and contraction, reducing the risk of cracking.
- It is challenging to prevent concrete from cracking or fissuring. Its thickness is considerable, as is its water content, resulting in greater shrinkage.
- Concrete finishes are typically more glossy.
- Concrete offers less protection; thus, it has lower stain resistance.
In Conclusion: Why opt for microcement?
In conclusion, having elucidated the disparities among polished concrete, polished cement, and ready-to-use microcement, the choice becomes clear. Ready-to-use microcement emerges as the preferred option owing to several pivotal factors, summarized below:
- Enhanced flexibility and resistance attributed to its unique composition.
- Simplified and adaptable application process devoid of extensive construction work or debris.
- Unparalleled customization and versatility in terms of textures and colors.
- Simplified maintenance and care regimen.
Are you persuaded? Do not hesitate to reach out to us for further inquiries!
Did you find this article interesting about the differences between polished concrete and ready-to-use microcement? Share your opinions on our social networks and send us your recommendations or results after application.